Unlocking Excellence: Key Concepts Covered in Lean Six Sigma Green Belt Certification
- a17803949
- Dec 11, 2023
- 2 min read
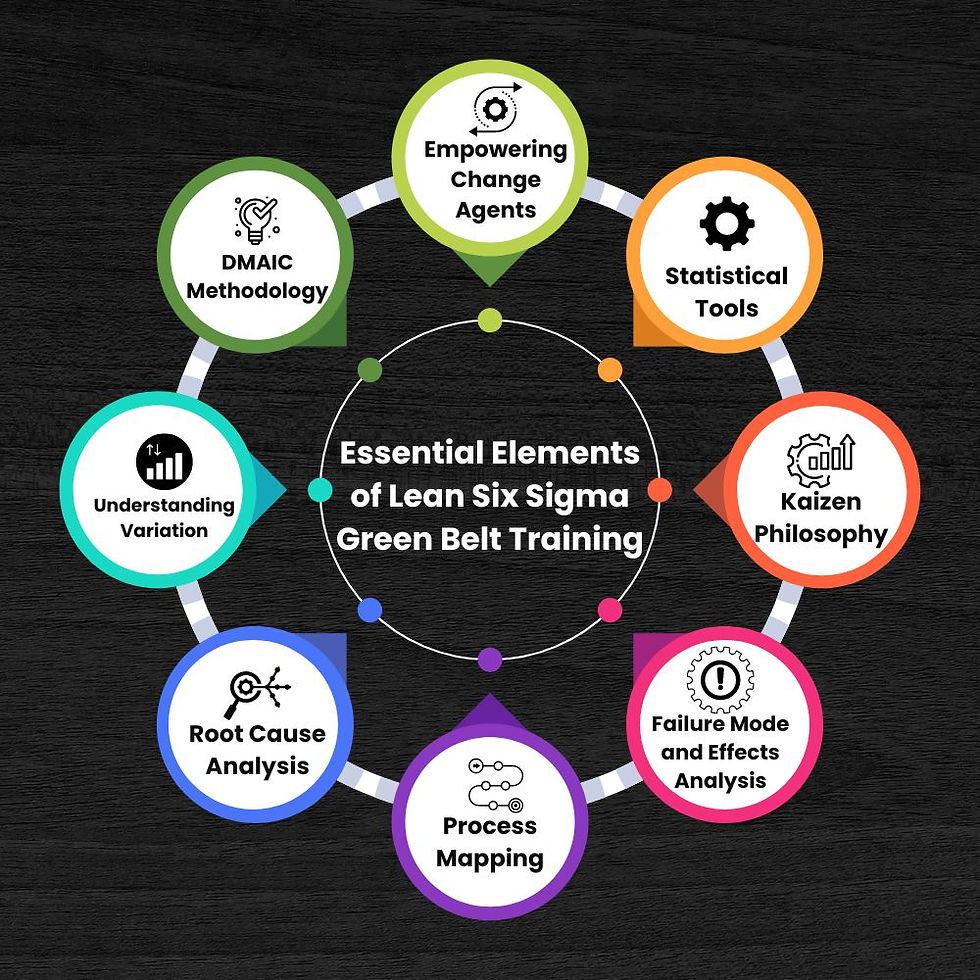
Introduction
In a dynamic business environment, organizations are constantly looking for ways to increase productivity, reduce waste, and deliver exceptional value to customers. Enter Lean Six Sigma, a powerful methodology designed to be appropriate. In this vein is green belt certification, a comprehensive training program that provides employees with the tools and skills to drive process improvement programs. Let's dive deeper into the key concepts covered in Lean Six Sigma Green Belt training, this the journey to productivity is not far off.
1. DMAIC Methodology: The Framework for Success
The DMAIC (Define, Measure, Analyze, Improve, Control) approach is central to Greenbelt training. This structured roadmap guides staff through each phase of the process improvement project. From measuring key performance indicators to defining project objectives to analyzing data, implementing improvements and ensuring continued compliance, DMAIC is a winning strategy.
2. Understanding Variation: The Enemy of Consistency
Variability in Lean Six Sigma processes is known to be the root cause of defects and inefficiencies. Green belt certification emphasizes the importance of understanding and managing change through accountability methods. Concepts such as standard deviation, control charts, and process capabilities help Greenbelts identify and systematically manage sources of nonconforming materials.
3. Root Cause Analysis: Digging Deeper for Solutions
An important aspect of Lean Six Sigma is the ability to identify and address the root causes of problems rather than simply treating the symptoms. Greenbelts learns a variety of tools including fish skeleton diagrams and the "5 Whys" approach to systematically explore the underlying issues affecting this operational performance These analytical skills are essential for sustainable development.
4. Statistical Tools and Techniques: Unleashing Data Power
Greenbelt training provides a solid foundation in the statistical methods necessary for effective decision-making. From basic descriptive statistics to hypothesis testing and regression analysis, Greenbelts develop the skills necessary to analyze data, derive meaningful insights, and make informed decisions for program improvement.
5. Process Mapping: Visualizing the Path to Improvement
A picture is worth a thousand words. Greenbelts learn how to draw process diagrams and flowcharts, which provide visualization of the process. This tool helps identify inefficiencies, redundancies and areas for improvement. Process mapping is key to its manageability and efficiency.
6. FMEA (Failure Mode and Effects Analysis): Proactive Risk Management
Lean Six Sigma Green Belt training provides employees with FMEA, a systematic approach to identifying and prioritizing potential process failures in the process. By anticipating and mitigating risks, Greenbelts helps create robust strategies that can meet the challenge, allowing them to continue to succeed.
7. Kaizen: The Spirit of Continuous Improvement
The philosophy of Kaizen, which means "change for the better" in Japanese, is embedded in Lean Six Sigma. Greenbelt training promotes a continuous improvement mindset, encouraging employees to look for incremental improvements in processes. This cultural shift fosters an environment where everyone is committed to making small positive changes regularly.
Conclusion: Empowering Change Agents
Lean Six Sigma Green Belt training goes beyond developing theoretical skills; It transforms individuals into change agents equipped with the skills to make meaningful progress in their organizations. As Greenbelts apply these core concepts to real-world projects, they help create a culture of excellence and efficiency. The journey to a Lean Six Sigma Green Belt isn’t just about getting certified; It is the promise of unlocking the full potential of strategies and, in turn, the success of an organization.
Comments